There are significant advantages of running newer engines when it comes to fuel economy. However, as we know it, not everyone has the resources to operate newer equipment. If you find yourself with older technology, this article articulates the best practices of maintaining these systems and explains why newer, more efficient tractors can be beneficial to your business. As author John Baxter says, after all, such knowledge does seem to make sitting at the coffee counter in a truck stop and conversing with other drivers more fun.
The First Common-Rail System: ACRS
Before 2007, American engine makers unanimously used camshaft-driven fuel injectors. However, in 2007, Detroit Diesel replaced the Series 60, and was enlarged to 14 Liters with the DD15. The DD15 had a revolutionary injection system called ‚"CRS" or Amplified Common Rail System.
Common rail was not an entirely new concept‚ such systems had been used on early diesels used on ships. But, unit injectors had taken over because of the high pressure they produce inside a solid metal body instead of a thin metal pipe. German engineers knew that the traditional injection forms were never going to cut it in the future, and they also knew that metallurgy (the science of making metals light and strong) had come a long way. They realized that a new injection system could solve the one inadequacy of unit injectors‚ their tendency to perform at best only at higher RPMs.
Unit injectors use plungers, like long pistons‚ to force fuel through the tiny holes or orifices drilled into the cup at the bottom of the unit. The plungers are driven downward by the camshaft driving rocker levers. This means that a certain amount of fuel flows into the engine for each, say, 3 degrees of crankshaft rotation, which fits with the original diesel idea of introducing fuel gradually as the piston descends. These injectors can do amazing things, and at RPMs approaching the 1800 RPM governed speed for engines of that era, they can quickly produce pressures well over 30,000 PSI (for pounds per square inch pressure). The high pressure accelerates burning and minimizes soot production. Low soot is especially hard to achieve with high levels of EGR, so high injection pressures are an important goal of diesel designers.
The problem is that a system like this loses a lot of its power when running the engine at low, fuel-efficient RPMs. A system that produces 35,000 PSI at 1800 RPMs will put out less than 25,000 PSI at 1,200 RPMs.
Enter Common Rail. The ACRS system had a powerful pump that produced about 13,000 PSI. It pumped fuel at a constant pressure into a rail, a pipe with about ¾ of an inch diameter. The rail was connected to the injectors in every cylinder.
The ACRS injectors used a different plunger with two sections‚ alarger diameter upper section and a smaller-diameter lower section. Fuel released at 13,000 PSI into a chamber above the top of the plunger would force it down when the ECM opened a valve to allow the fuel in and start the injection. The chamber below the plunger also had fuel and the typical arrangement of small holes at its bottom. Because the bottom of the plunger was of a smaller diameter, the force was concentrated and the injector could deliver up to 38,000 PSI injection pressures. The system was designed so the valve that let the fuel into the upper chamber could throttle the fuel and produce "rate-shaping", which meant the injector could pump in fuel at a lower rate and soften the beginning of combustion and the early stages of burning. This helped reduce peak cylinder pressure and temperature and reduce Nox. After the piston began to descend, it would open fully if necessary to rapidly burn the fuel as the piston started moving downward to produce maximum power.
Such a system can also stop and start injection to spread out the burning while maintaining fuel pressure to ensure good combustion. The conditions change with load and RPM.
The MaxxForce
Shortly after, also in 2007, Navistar introduced the MaxxForce engines, including the N13, an engine for Class 8 trucks. Many of the engine's components came from MAN, a German manufacturer that had been the very first to license the original diesel patents. They provided a cylinder block of a lighter iron known as Compacted Graphite Iron. The engine had a slightly different form of common-rail system that did not amplify the pressure inside the injector but utilized piping to withstand the full pressure throughout the system. Partly because of its advanced injection system, the engine could produce peak torque down to 1,000 RPM when most engines could not do this below 1,200 RPM. Both injection systems are described below along with the system that Cummins adopted, as they have a similar design.
2010
In 2010 all the manufacturers were required to meet significantly lower Nox standards, which dropped by nearly 90%. Cummins was one engine maker that tried to meet the standard with internal engine changes. Still, in the end, they adopted what the majority of the industry went to, a process called Selective Catalytic Reduction. SCR uses DEF or Diesel Exhaust Fluid to mix inside a catalytic chamber at high temperatures with the engine's exhaust. This chamber follows the DPF, and thus is located where the burning off of the soot has increased exhaust heat, which helps SCR work.
The DEF contains urea, a chemical that turns to ammonia in the SCR catalytic chamber. The ammonia then combines with the Nox (Nox refers to nitrogen-oxides, a combination of nitrogen from the air with oxygen) in the exhaust to form harmless nitrogen and water. Cummins found a unique copper zeolite catalyst they claimed made the SCR process more efficient and decided to join the rest of the entire industry, except for Navistar, in relying on SCR to meet the 2010 Nox standards. The challenge with meeting Nox standards in the cylinder is that the burning fuel can't get too hot, which works against engine efficiency and other aspects of clean-burning.
In addition, as mentioned above, Cummins’ competitors, both Detroit Diesel, and Navistar with its MaxxForce engines, already had common-rail injection. So, Cummins worked with Scania, a Swedish company, to develop their XPI common-rail system.
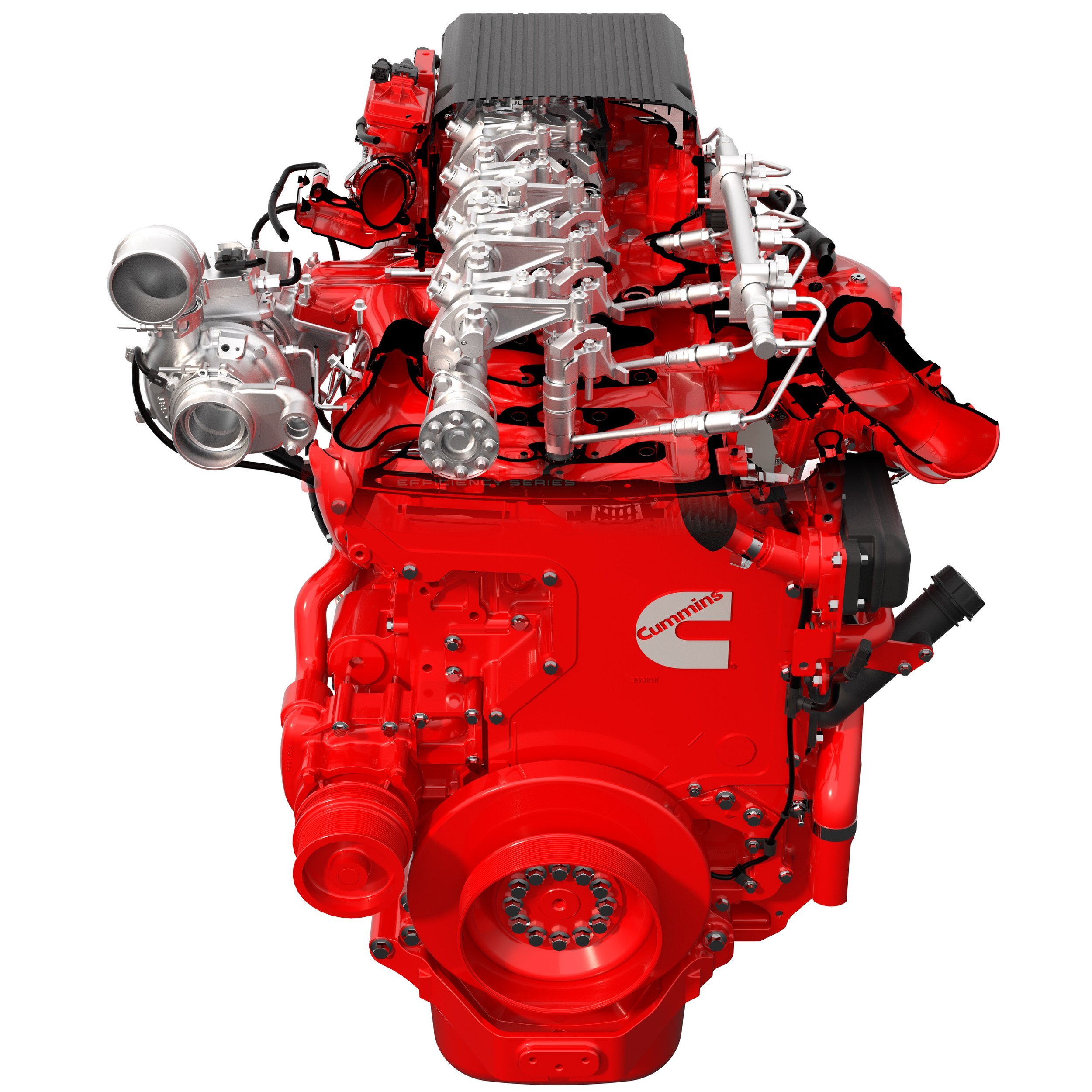
The interesting system Cummins was using before 2010 had the advantage of offering a slightly softer start of combustion, but it was incapable of any form of split injection. Meeting 2010 necessitated breaking each injection cycle into several separate shots to keep the cylinder from getting too hot. It also required pilot injection—a small spurt of fuel well before maximum compression that didn’t ignite, but set the stage for immediate ignition of the main fuel charge once injection began. The best common-rail systems could both soften the start of combustion with pilot injection (and do it even more effectively than the Cummins open cup system), and stage it in separate pulses to keep the burning fuel charge from getting too hot. Hence the decision.
How Common-Rail Systems Work
So what do these common-rail systems look like? Although diesel fuel, as a liquid, is hard to compress, it is just slightly elastic. So, with stronger metal piping available than ever before, engineers designed a fuel rail, a long, relatively large-diameter pipe (more than half an inch) that was much larger than the piping previously used on diesel injection systems. This pipe runs the length of the engine and communicates with an injection valve in each cylinder that has an electrical needle valve. These valves can be rapidly opened and closed by the ECM. The pipe would be fed by a crankshaft-driven pump with several pistons that would alternately pump the fuel into the rail system continuously and smoothly. The pump would be controlled much as injection had been controlled in electronic unit injectors‚ electric valves would be opened and then closed when the pistons were rising and forcing fuel out of the pump and into the piping leading to the rail. The difference was that the pumping would be continuous rather than occurring only for a few degrees as the piston went over the top at the beginning of each power stroke.
If more fuel were needed, the valves would be closed longer, and, as when the driver gets up to cruising speed on a highway and draws back on the throttle to cruise, the valves would start closing after a shorter stroke of each piston. A sensor that measured rail pressure would send a pressure signal to the ECM to continuously monitor the pressure and keep it at the desired level. In this way, the pressure in the rail could be kept constant. Although there would be small pressure changes or "pulses" each time each injector is fired, only one injector fires at a time, and the amount of fuel injected each time a valve opens is minimal compared to the rail volume that the pressure remains stable.
There would also be a pressure relief valve like the safety valve on a boiler to release excess pressure if the electronics were not controlling the pressure well enough or there was a sensor failure. But, the bottom line is that, with this kind of system, the ECM could produce the desired fuel pressure at all times, even when the engine was idling.
The Advantages of Common-Rail Systems
Being able to draw fuel out of a rail at 30,000-35,000 PSI at all RPMs is a diesel engineer's dream. The issue here is that the former unit injector systems could not provide maximum pressure down to the engine's torque peak, which is at 1,200 RPM or lower. With the earlier systems, while the fuel was actually sent in at an appropriate rate, the pressure drop still meant poorer mixing with the air in the cylinder. This meant more soot emissions, limits to low-rpm torque, and how slowly the engine can turn and still deliver good fuel economy and performance.
Fewer Particulate Emissions
Today's common rail sends the fuel in at maximum pressure, or whatever pressure is needed, even at 1,000 RPM or less. And, because the electrically-powered needle can break the injected shot of fuel into several separate pieces, the system can still keep the pressure in the cylinder from rising too fast and to too high a level. This helps with Nox emissions and keeps engine stresses within limits. Being able to send the fuel in over the same period of time, but in perhaps 3 high-pressure spurts, rather than one lower pressure spurt, also meant fewer particulate emissions because the fuel was more effectively atomized and mixed with the air. As you might imagine, if your fuel is protected from gelling, this system will start your engine even at frigid outside temperatures.
Cooler Cylinder & Quieter Engine
The system can also drop its pressure somewhat in order to pump the fuel in more gradually and keep the cylinder even cooler (keeping the peak pressure and the Nox-producing peak temperatures much lower) when the truck is cruising, when the required power and torque are much lower. This also makes the engine quieter.
Lower Engine Weight & Horsepower
Additionally, because the common-rail pump forces fuel in continuously, merely maintaining rail pressure, the violent rise and fall in pressure and almost violent fluctuations in torque necessary to drive a camshaft that powers unit injectors go away. In fact, where camshafts were adapted to just operating the valves, or in Cummins' case where the separate injector camshaft went away entirely, as much as 200 lb. of weight was taken out of the engine. The horsepower needed to drive the fuel system also was lowered. It takes less than 15 hp to drive a common-rail pump. And, the common-rail pump means setting the overheads involves only adjusting the valve rockers.
The Paccar MX13 engine came out in 2010. This engine has an in-block camshaft to lower its profile. It used unit pumps to send the fuel to its injectors for several years, one for each cylinder. These high-performing pumps had electric delivery valves so there were valves in both the injectors and the pumps (at both ends of the short, fat supply lines) to ensure more precise performance. However, in 2013, Paccar developed a common-rail system. The only difference from the Navistar and Cummins systems was that it used two unit pumps driven off the camshaft to feed the rail via shorter lines than those used with crankshaft-driven pumps. The engine uses two-unit pumps‚ enough to provide smooth operation.
Volvo had a robust and high-performing form of unit injector driven by its camshaft until 2017. These performed exceptionally well at low RPM because they had two control valves, one to supply the injector and one to relieve pressure, rather than just one. The valves' operation could be coordinated and the fuel supply throttled in such a way as to maintain enough pressure for good performance at low rpm, and yet ensure maximum performance at governed RPM.
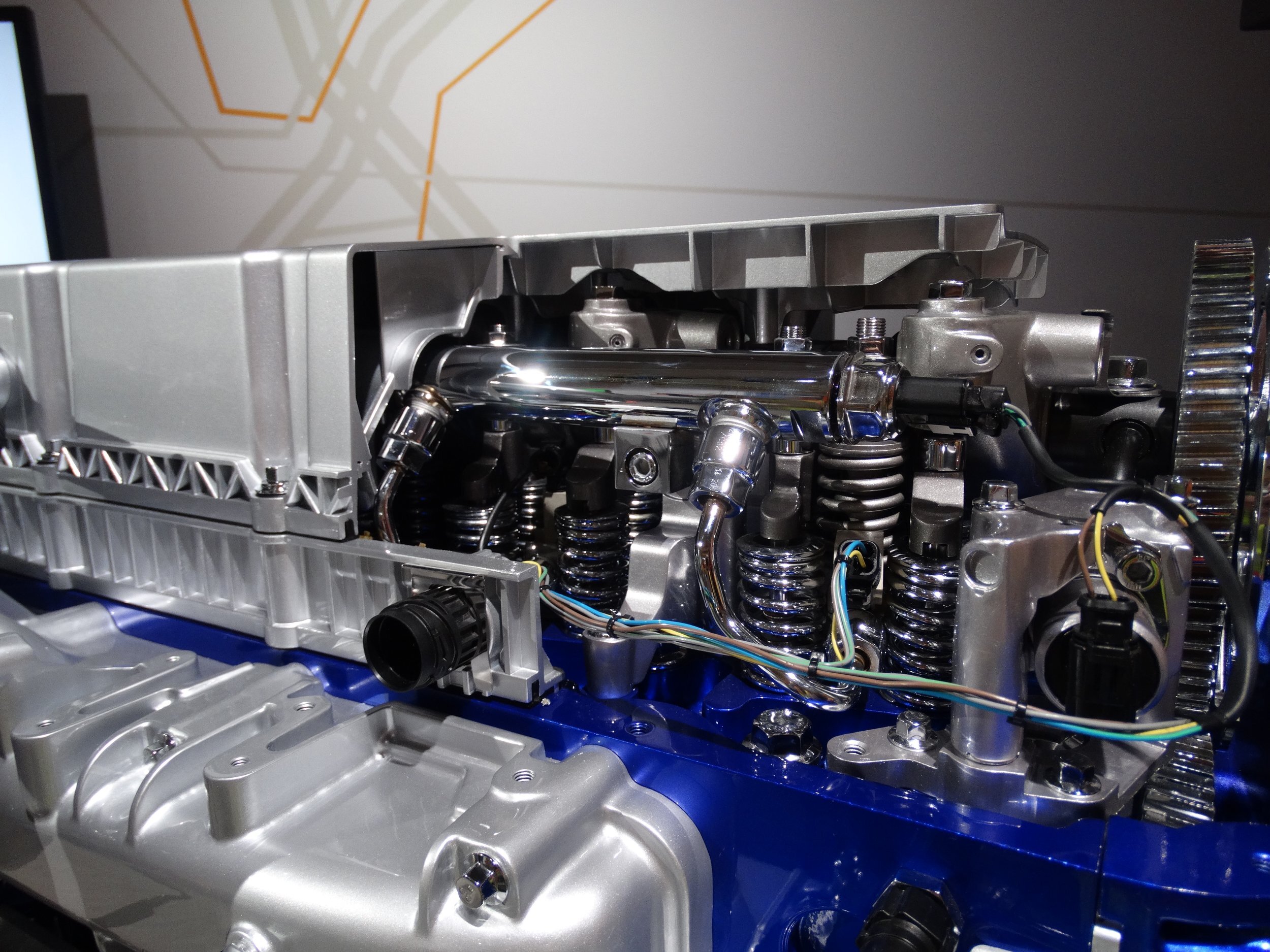
But, in 2017, Volvo went to a common-rail system with the rail housed under the cam cover. As shown above, they cleverly designed a system where three of the six injectors are combined with unit pumps driven off the camshaft. The pumps use common lines connecting those three injectors to the rail to both feed the rail at some times, and send fuel back to those three injectors at other times. The new system is quieter than the old one, and can break the fuel charge sent to each cylinder into smaller pieces than before. This is the only common-rail system where rockers driven off the camshaft drive the unit pumps and need to be adjusted with the valves when running the overheads. This change was accompanied by adopting their "Wave piston" that has protrusions in the combustion chamber wall that send the sprays of fuel back toward the chamber center, thus preventing pooling of fuel on the chamber walls and soot. The new piston permitted the compression ratio in Volvo engines to increase one point to 18:1. Since the Mack MP8 uses a similar architecture, although having different torque and power curves, their engine shares this newer technology.
Down-Speeding
The real payoff of all this is "down-speeding" originated by Volvo. Having an injection system that can offer ideal pressure at and even below 1,000 RPM, combined with the superior aerodynamics of the latest tractors, means that cruise RPMs keep dropping. Before turbocharging, many diesels were supposed to cruise at beyond 1,800 RPMs. As injection systems developed, cruise RPM dropped to 1,600, then 1,500, then 1,300, depending on the size of the engine.
But with automated transmissions handling the occasional downshifts that may be needed on typical Interstate highways, and with combustion being ideal even down to 900 RPM, the latest trucks now cruise at 1,150, or even just over 1,000 RPM. Volvo's latest offering employs a turbo-compounding concept that uses a second turbine to recover exhaust energy after the turbocharger and drive the crankshaft. The engine can develop maximum power and torque with less fuel going into the cylinders. The resulting lower cylinder loads allow cruise RPM at or below 1,060 RPM.
Final Thoughts
Since low RPMs help the engine breathe more easily, reduce friction, and make better use of the combustion energy, which has trouble keeping up with the piston at higher RPMs, down-sped powertrains are saving many truckers and small trucking companies a lot of money on their fuel bills. They also give the driver a quieter ride. But, without common-rail injection, this would not be possible.